Which is better- Recycled or Upcycled Fabric for Outdoor Gear and Clothing
Author
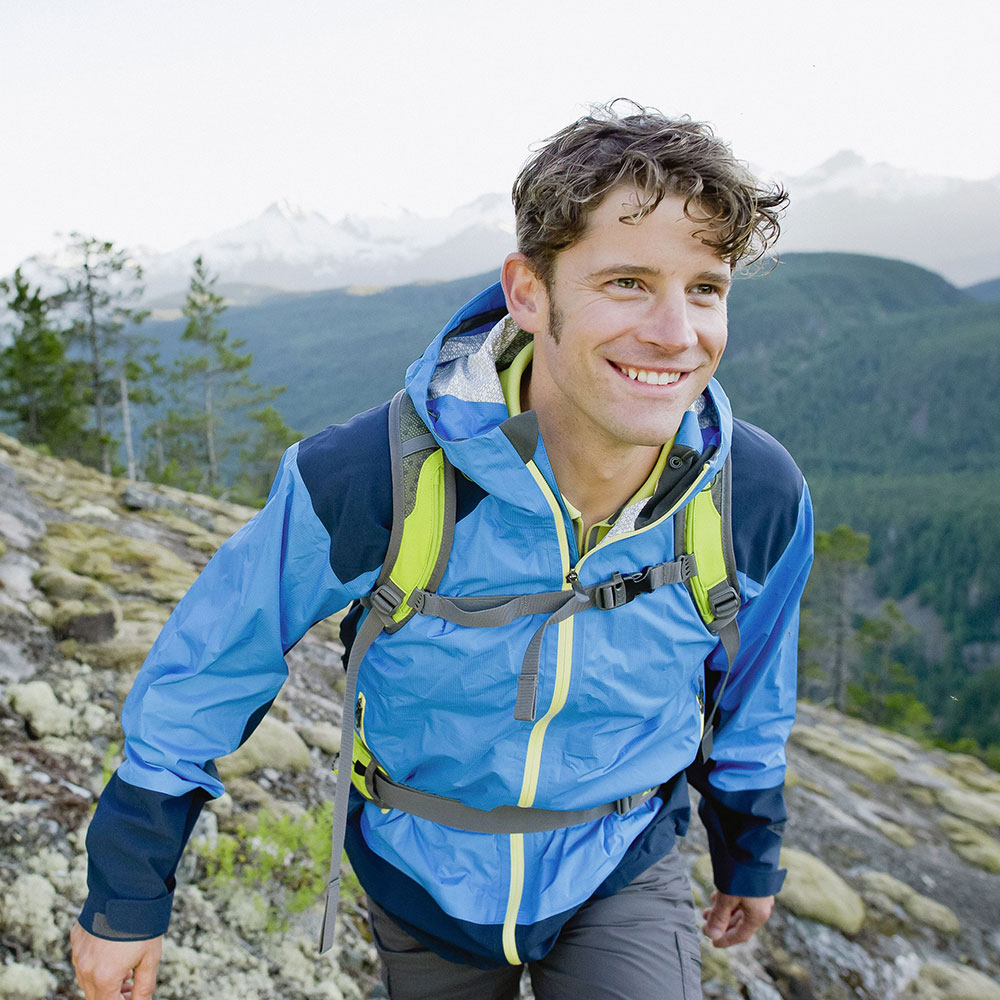
Mike has a real passion for cycling, hiking and just generally being outdoors. Being from Warrington, he is only a few hours away from North Wales, The Peak District, Yorkshire and the Lake District. He has climbed Mount Kilimanjaro and done a lot of the mountains in the Lake District. His new passion is walking his dog and enjoying a pint at the end.
Tons of outdoor gear and clothing come up every year in the market. But the interesting thing that is brewing in the market is the range of eco-friendly and sustainable products that are being sold. Products made from recycled fabrics, organic cotton, and hemp were being marketed and sold this year as well with increased hype. The industry is heading towards a more environment-friendly and sustainable outlook. And even though it’s a great initiative, there are some drawbacks to it as well. The major one is the process of recycling which puts huge pressure on the environment.
I came across this Portugal-based company called Truce Design which sells eco-friendly backpacks. They make their backpacks from upcycled materials like old sailcloth and drysuit fabric. I was fortunate enough to share a conversation with the founder of Truce Designs, Luke Mathers where he spoke about the true meaning of sustainability and the issues that come with using recycled plastic fabric.
Luke Mathers's take on recycling v/s upcycling
Through this article, I want to discuss and make everyone reading this aware of the differences between upcycling materials and recycled PET and other plastic materials that companies use to make new products.
Annually the apparel and accessory industry produces around 21 billion pounds of waste. What my company, Truce Designs does is take out the unused and reusable materials from the drysuit factories and buy excess fabric rolls from the warehouses. In this manner, we try to do our bit in conserving the environment by not using many virgin materials as we would use ideally. However, making buckles, zippers, and trim are difficult to source from upcycled materials.
To be honest, scaling a sustainable business like Truce’s is difficult to achieve without some compromises in standards.
The Recycling of Plastic into Yarn
Upcycled and recycled materials are completely different processes but may often come across as used interchangeably. We take the example of Polyethylene terephthalate (PET) material which is made from plastic water bottles.
Process
By the time a plastic bottle reaches a recycling centre, it is usually sterilized, dried, and crushed into small chips. Then, it is heated through a spinneret machine that converts the material into yarn. This yarn is then wounded, crimped, baled, dyed, and knitted into a new fabric roll. After that, the fabric is dyed, coated, and given a nice finishing. While performing these last processes, a lot of toxic chemicals are released. To handle them properly, one needs to have certain standards and that’s when Bluesign®, etc, comes to help.
Impacts
Any process uses a lot of energy and human labour. However, recycling is any day better than using fresh petroleum products to make new polyester and nylon. The process involves a lot of time, water, energy, and labour and produces a lot of waste. It also exposes the labourers to hazardous conditions. Moreover, PET was not designed to be close to human skin and sweat as its fibres contain UV stabilizers and dioxins which have adverse effects on living organisms.
Upcycling of Fabrics
At our company, we use old sails that have been used for a long time on the water. The hardware is cut off from the sail and the pieces are washed with soap. Dry them and you can start making your backpack from this material.
However, there is still waste created by us. We are not always perfect and often discard materials that are doubtful to retain a good quality product. Moreover, as previously mentioned that it is difficult to source zippers, buckles, etc. from upcycled materials and hence, we have to get fresh pieces that are not very sustainable.
Author
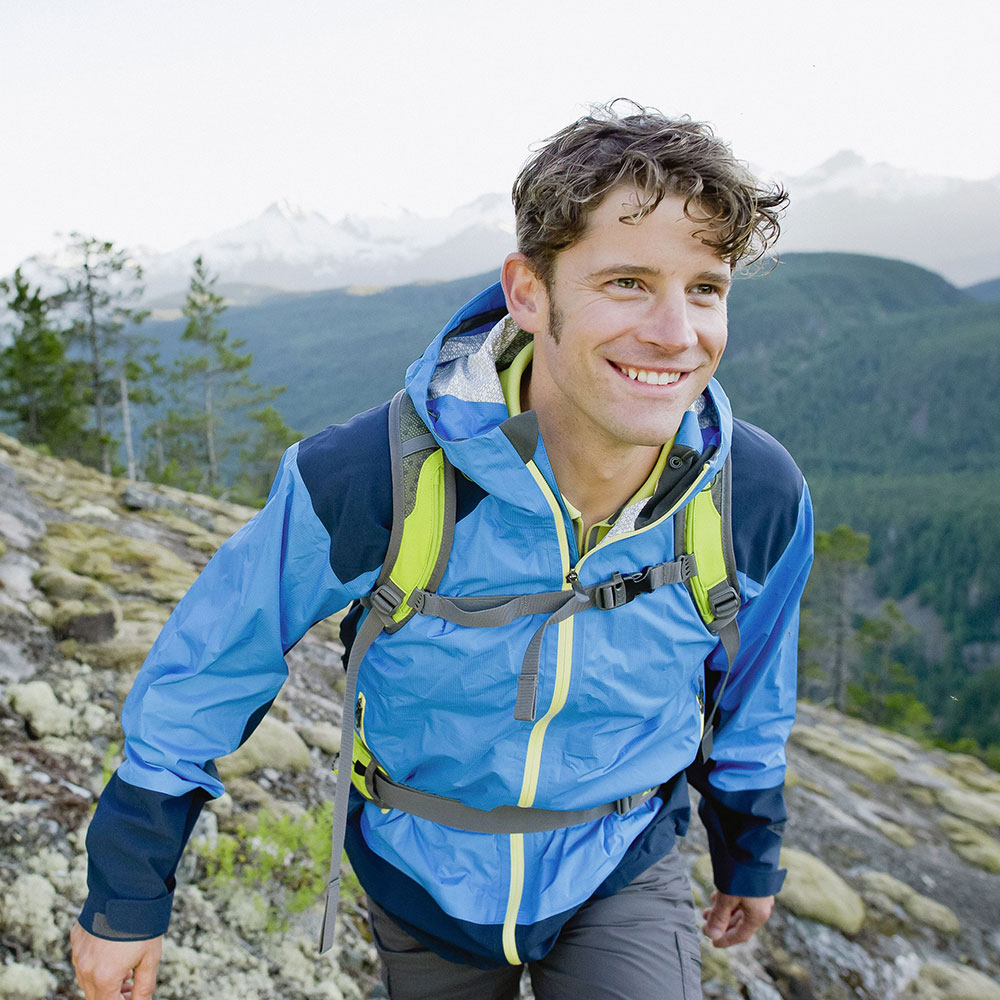
Mike has a real passion for cycling, hiking and just generally being outdoors. Being from Warrington, he is only a few hours away from North Wales, The Peak District, Yorkshire and the Lake District. He has climbed Mount Kilimanjaro and done a lot of the mountains in the Lake District. His new passion is walking his dog and enjoying a pint at the end.
Categories
- Sport (28)
- Product Reviews (3)
- Team Outdoor Look (7)
- Mike Wild (2)
- Mike Payton (2)
- Suse Hammond-Pears (3)
- Snowboarding (12)
- Latest Offers (105)
- Shop Talk (1)
- Competitions (7)
- Walking (413)
- Lifestyle Fashion (8)
- Travel (86)
- Kit Guides (176)
- Workwear Clothing (6)
- Safety Workwear (4)
- Health/Fitness (289)
- Skiing (91)
- Great Outdoors (1316)
- Cycling (92)
- January 2025
- December 2024
- November 2024
- October 2024
- September 2024
- August 2024
- July 2024
- June 2024
- May 2024
- April 2024
- March 2024
- February 2024
- January 2024
- December 2023
- November 2023
- October 2023
- September 2023
- August 2023
- July 2023
- June 2023
- May 2023
- April 2023
- March 2023
- February 2023
- January 2023
- December 2022
- November 2022
- October 2022
- September 2022
- August 2022
- July 2022
- June 2022
- May 2022
- April 2022
- March 2022
- February 2022
- January 2022
- December 2021
- November 2021
- October 2021
- September 2021
- August 2021
- July 2021
- June 2021
- May 2021
- April 2021
- March 2021
- February 2021
- January 2021
- December 2020
- November 2020
- October 2020
- September 2020
- August 2020
- July 2020
- June 2020
- May 2020
- April 2020
- March 2020
- February 2020
- January 2020
- December 2019
- November 2019
- October 2019
- September 2019
- August 2019
- July 2019
- June 2019
- May 2019
- April 2019
- March 2019
- February 2019
- January 2019
- December 2018
- November 2018
- October 2018
- September 2018
- August 2018
- July 2018
- June 2018
- May 2018
- April 2018
- March 2018
- February 2018
- January 2018
- December 2017
- November 2017
- October 2017
- September 2017
- August 2017
- July 2017
- June 2017
- May 2017
- April 2017
- March 2017
- February 2017
- January 2017
- December 2016
- November 2016
- October 2016
- September 2016
- August 2016
- July 2016
- June 2016
- May 2016
- April 2016
- March 2016
- February 2016
- January 2016
- December 2015
- November 2015
- October 2015
- September 2015
- August 2015
- July 2015
- June 2015
- May 2015
- April 2015
- March 2015
- February 2015
- January 2015
- December 2014
- November 2014
- October 2014
- September 2014
- August 2014
- July 2014
- June 2014
- May 2014
- April 2014
- March 2014
- February 2014
- January 2014
- December 2013
- November 2013
- October 2013
- September 2013
- August 2013
- July 2013
- June 2013
- May 2013
- April 2013
- March 2013
- February 2013
- January 2013
- December 2012
- November 2012
- October 2012
- September 2012
- August 2012
- July 2012
- June 2012
- May 2012
- April 2012
- March 2012
- February 2012
- January 2012
- December 2011
- November 2011
- October 2011
- September 2011
- August 2011
- May 2010
- April 2010
- March 2010
- February 2010
- January 2010
- November 2009
- October 2009
- September 2009
Submit a Comment